The elevating work platform (EWP) was purposely designed and engineered to keep the hydraulic and electrical system simple and accessible for easy servicing and maintenance. Based on the reliable cable suspension system, the platform is powered by a hydraulic system and controlled by a hand-held remote transmitter.
Each platform is custom designed to suit the existing service pit and the individual requirements of the workshop. An assessment is recommended when retrofitting an existing pit with an EWP. A deeper pit will gain the full benefits of an EWP.
Contact us for further details on the technical specifications of the platform.
Watch full video demo (6 mins)
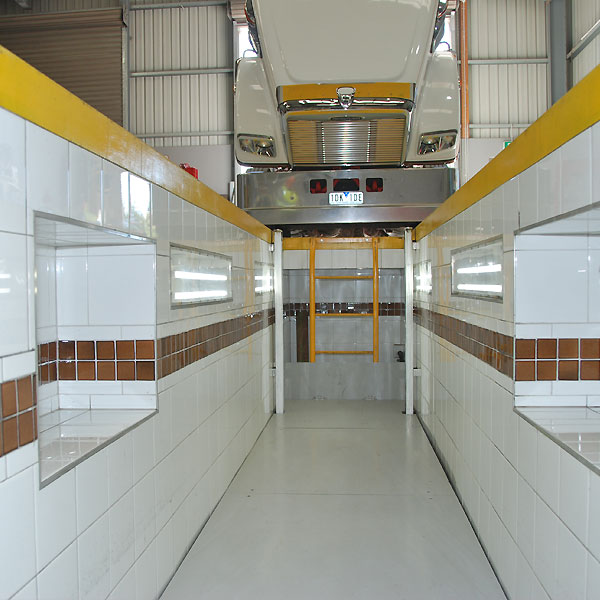
How does it work?
The platform is supported and guided by posts bolted to the inside walls of the pit. The platform operates via a series of cables which are connected to a hydraulic ram. The hydraulic ram is seated horizontally within the platform frame and moves with the platform. When the ram is fully retracted, the platform is at its highest position, level with the workshop floor.
As the platform is lowered, the ram extends increasing the cable length. The hydraulic system allows an infinite adjustment to the platform height within the pit.
Platform standard thickness ranges from 125 – 200mm and can be built with a grated floor cover for wet pit operations or from materials to suit your application.
SAFETY FEATURES
Electrical
The circuitry is designed and built to Australian Standards Category III AS4024 which dictates high-quality components and emergency deactivation.
Hydraulic
The counter-balance valve on the hydraulic ram prevents the platform from descending should a hydraulic hose fail. This valve also prevents any hydraulic creeping.
Maximum Rated Capacity (MRC)
If the platform MRC is exceeded, a controlled gradual descent of the platform is initiated to a height more appropriate to the load.
Platform support cables
Should one of the support cables fail, the remaining cables are able to support the platform load as each cable is break-test rated to a load capacity 5 times that of the total MRC.
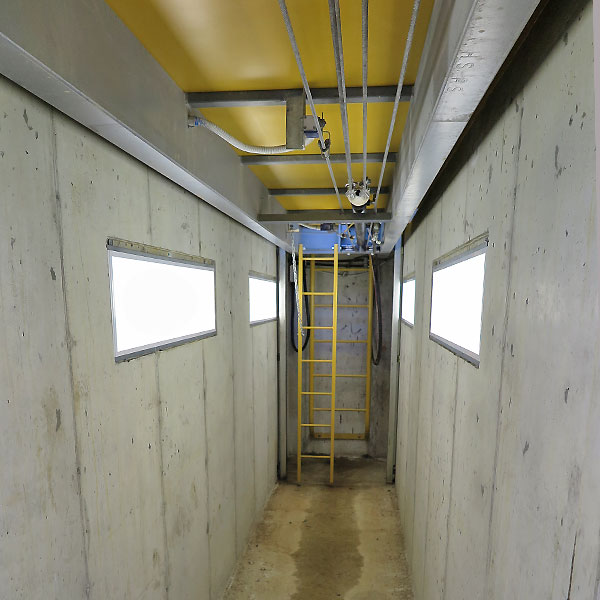
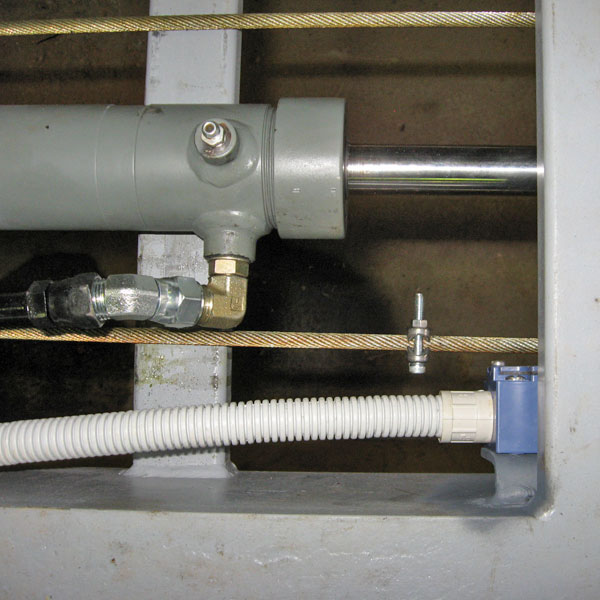
Activation of platform
The accidental activation of the platform is prevented due to the dual control circuitry (2 switches need to be pressed and held simultaneously).
Platform obstructions
(1) Rope tension switches activate if any restriction is detected during platform descent eg objects in pit base.
(2) Photoelectric sensors detect the presence of objects protruding past platform edge during ascent (optional).
Radio interference
If any radio interference is detected, the transmitter and receiver will automatically switch radio channels (AS CAT III remote) or deactivate the platform (AS CAT II remote).
Alarms
Two (2) alarms are activated when the hydraulic platform system is in use; an audible alarm and a flashing light.
All systems need to be operational for the platform to move.
RADIO TRANSMITTER & RECEIVER
The EWP hydraulics are controlled by a hand-held radio remote transmitter. The “standard” remote transmitter will deactivate the platform if radio interference is detected. The “hazardous environment” remote transmitter will automatically switch radio channels should radio interference be detected.
The EWP control panel houses the radio remote receiver, an emergency stop for the EWP, an isolation switch and alternate controls for the EWP. The panel is mounted next to the hydraulic power pack, usually located in an area off to the side of the workshop. The EWP is connected to these with 24V cabling and hydraulic plumbing housed in underground conduit, eliminating cables/hoses across the workshop floor.
An auto-activated switch circuit (activated by EWP) is installed with 3 relays available as standard. These can be utilised for lighting, ventilation fans etc.
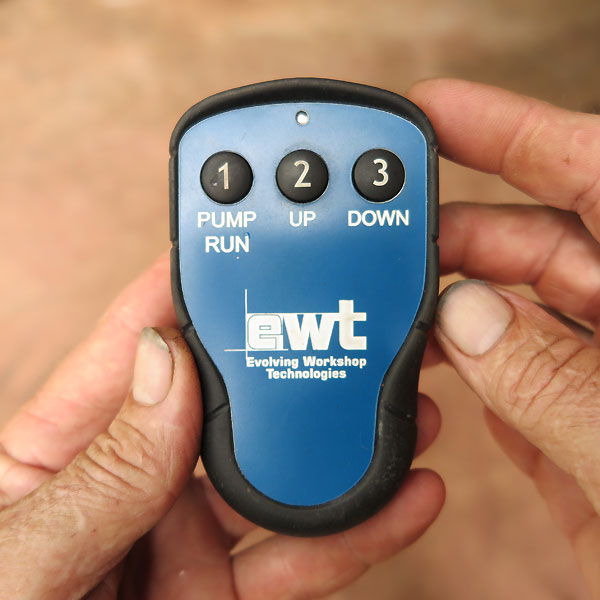
Hand-held remote transmitter used to control the EWP
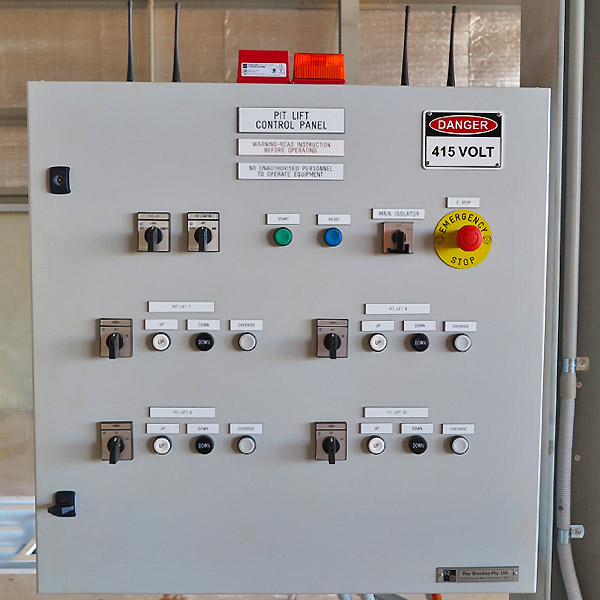
Control panel for the EWP (Panel shown controls 4 independently operated EWPs in two pits)
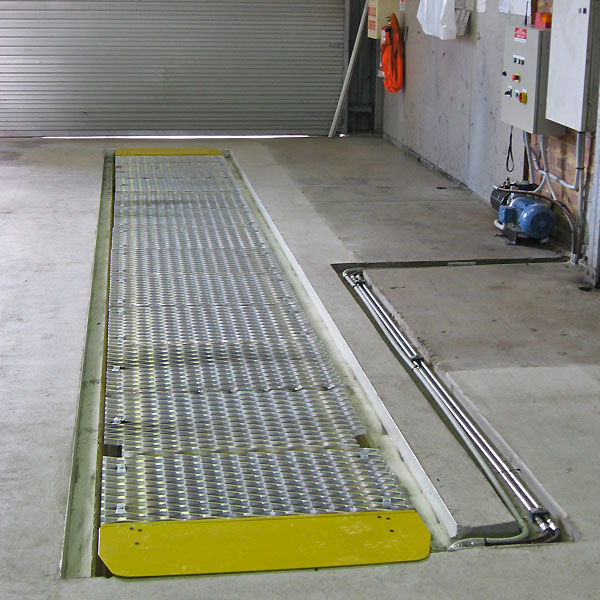
Photo showing underground electrical cabling (24V) and hydraulic hoses connecting the EWP to the control panel prior to covering
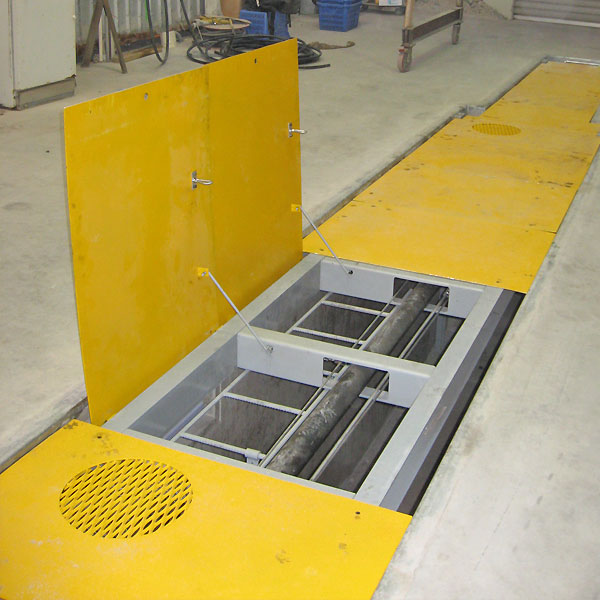
MAINTENANCE
The hydraulic plumbing, electrical cabling and pit base are accessible from the personnel access panel (a hinged section of floor plate) on the platform. A swing-down ladder built into the platform frame allows quick and easy access for maintenance and servicing the EWP and for cleaning the pit base. The swing-down ladder also acts as a safety prop during these procedures.
Users only require minimal training and workshop staff can easily follow the maintenance schedule. No annual certified inspection required. Parts, if required, are non-specific and should be available locally from hydraulic, electrical wholesalers and/or lifting gear suppliers.
DURABILITY
The EWP has demonstrated to withstand the toughest conditions since 2006. Proven to operate in environments with oil, grease, and debris.
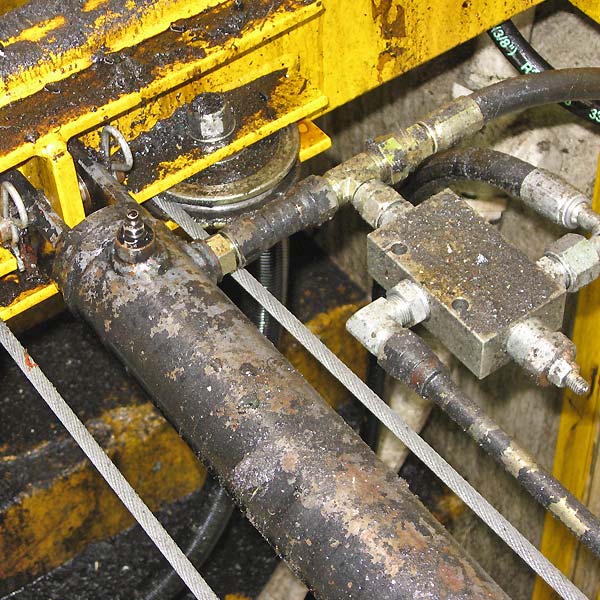